How Leadership Drives a Culture of Quality in Manufacturing: 7 Examples
In a rapidly evolving manufacturing landscape, the role of leadership in fostering a culture of quality cannot be overstated. This article explores how prioritizing quality across all levels and recognizing and rewarding quality achievements contribute to this goal. With insights from seven key perspectives, readers will gain a comprehensive understanding of effective leadership in driving quality. Discover actionable strategies and real-world examples that highlight the transformative power of strong leadership in manufacturing.
- Prioritize Quality Across All Levels
- Engage Directly with Teams
- Set Clear, Measurable Quality Goals
- Champion Quality to Inspire Employees
- Foster Open Communication
- Invest in Employee Training
- Recognize and Reward Quality Achievements
Prioritize Quality Across All Levels
Leadership plays a pivotal role in driving a culture of quality within a manufacturing organization. A culture of quality is not just about adhering to standards or processes—it's about embedding quality into every aspect of the organization's operations, from product design and production to customer interactions.
Effective leadership ensures that quality is prioritized across all levels of the organization, and employees are empowered to take ownership of the processes.
Here are some key ways leadership drives a quality-focused culture:
1. Vision: Leadership defines what quality means for the organization and aligns this vision with business objectives. By clearly communicating the importance of quality and making it a core value, leaders inspire the workforce to embrace it as part of their daily responsibilities.
2. Empowerment: Leaders empower employees by giving them the authority and tools to uphold quality standards. This includes fostering an environment where employees can voice concerns. Accountability is established through clear expectations and by recognizing those who consistently deliver high-quality work.
3. Continuous Improvement: Effective leaders champion continuous-improvement initiatives, ensuring the organization evolves with new technologies and methodologies.
4. Lead by Example: Leaders who demonstrate commitment to quality set an example for others even when they may not be actively involved in process improvements.
A prime example of leadership driving quality is Toyota's famed Toyota Production System (TPS). The leadership at Toyota, especially executives, instilled the philosophy of "Kaizen" (continuous improvement) and "Jidoka" (automation with a human touch). Leaders were committed and deeply involved in promoting a culture where every employee was responsible for the quality of the product.
In practice, if a worker spotted a defect on the assembly line, they were empowered to stop the line. This was unheard of in many manufacturing plants at the time. This leadership decision sent a powerful message that quality would never be compromised. This empowered employees to take pride in their work and helped Toyota establish its reputation for producing highly reliable, high-quality vehicles.
This shows how leadership can transform a manufacturing organization by creating a culture where quality is embedded in every process, empowering employees.
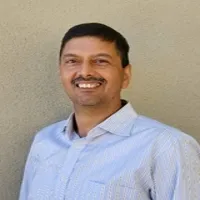
Engage Directly with Teams
In my experience as a PR professional working with manufacturing companies at the C-level, leadership plays a pivotal role in driving a culture of quality. It starts at the top, with executives setting the tone and expectations for the entire organization. Leadership must not only prioritize quality in their messaging but also embody it in their actions—making it clear that quality isn't just a goal, but a core value.
For example, one of my clients in the packaging industry implemented a company-wide initiative focused on quality improvement led by their CEO. Rather than treating it as just another directive, the CEO personally engaged with teams on the factory floor, listened to their feedback, and worked with management to implement practical changes.
By being visible and directly involved, the leadership demonstrated a commitment to quality that resonated throughout the organization. As a result, employees felt more accountable, and quality metrics improved significantly, not because of mandates but because the leadership inspired a shared belief in the importance of quality. This kind of hands-on, transparent leadership sets the standard for a culture that embraces continuous improvement.

Set Clear, Measurable Quality Goals
Setting clear, measurable quality goals from the top creates a roadmap for the entire organization. When leaders provide specific targets, employees understand exactly what to aim for. These goals also help track progress and identify areas needing improvement.
Consistent communication about these objectives ensures everyone stays aligned. This practice helps drive accountability and performance across all levels. Embrace this approach to elevate your company's quality standards.
Champion Quality to Inspire Employees
When leaders champion quality, it inspires the workforce to take ownership of their roles in maintaining it. By demonstrating a commitment to excellence, leaders encourage employees to invest in their work. This creates an environment where everyone feels responsible for the product's quality.
Such inspiration fosters a collective drive towards achieving higher standards. It also makes quality an integral part of the company's identity. Start championing quality to inspire and empower your team.
Foster Open Communication
A culture of open communication enables employees to identify and address issues proactively. Leaders who foster such an environment make it easier for employees to share ideas and solutions. Open dialogue reduces misunderstandings and promotes a sense of shared purpose.
By encouraging employees to speak up, leaders can pinpoint problems early and solve them efficiently. This approach minimizes disruptions and maintains a high level of quality. Promote open communication to build a strong, quality-focused workforce.
Invest in Employee Training
Investing in employee training and development ensures that quality remains a priority. When leaders allocate resources for skill enhancement, they signal the importance of continual improvement. Well-trained employees are more competent in their tasks and can better understand the complexities of production quality.
Training programs also keep employees updated on the latest industry standards and technologies. This proactive investment in people reflects a commitment to long-term quality. Commit to ongoing training to sustain and elevate quality in your processes.
Recognize and Reward Quality Achievements
Recognizing and rewarding quality achievements reinforces their importance within the organization. Leaders who acknowledge the hard work and ingenuity behind quality improvements motivate their team. Recognition can take many forms, from verbal praise to tangible rewards, but the key is consistency.
Celebrating successes builds morale and encourages others to strive for excellence. It creates an atmosphere where quality is both visible and valued. Implement a recognition system today to highlight and encourage exceptional quality efforts.