How Do Manufacturing Engineers Tackle Significant Production Bottlenecks?
When production hits a snag, strategies to overcome bottlenecks become invaluable, as a Director with firsthand experience reveals. Alongside expert insights, we've gathered additional answers that span from automation to predictive maintenance. From prioritizing orders and retrofitting machinery to enabling more efficient operations, discover the diverse tactics that have successfully navigated production challenges.
- Prioritize Orders and Communicate Delays
- Streamline Tasks with Automation
- Optimize Workflow with Lean Principles
- Increase Capacity by Retrofitting Machinery
- Enable Parallel Operations for Efficiency
- Prevent Bottlenecks with Predictive Maintenance
Prioritize Orders and Communicate Delays
We recently had a significant manufacturing delay due to limited raw materials being supplied. We knew that we wouldn't be able to keep up with the planned levels of production, so we had to prioritize. We did this by looking at outstanding orders, delivery deadlines, and production times. By being able to identify the most-ordered and most urgent items, we not only had an action plan in place to utilize existing resources most efficiently, but we also had clear information as to when the delayed items would become available. This allowed us to clearly communicate with affected customers and helped us avoid what could have been a much more significant setback.
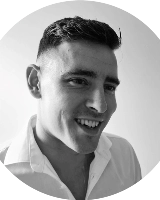
Streamline Tasks with Automation
Manufacturing engineers often turn to automation as a strategic tool to enhance efficiency and alleviate bottlenecks. By incorporating robotic systems or automated technology, repetitive and time-consuming tasks are streamlined, which can significantly increase production rates. This approach not only speeds up manufacturing processes but also improves product consistency and quality.
Automation enables the reallocation of human resources to more critical, higher-value tasks within the manufacturing pipeline. If your production line struggles with delays, consider exploring the various options for automation to boost efficiency.
Optimize Workflow with Lean Principles
Lean principles are a cornerstone for manufacturing engineers looking to optimize workflow and eliminate production slowdowns. By systematically analyzing the production process, engineers can identify wasteful activities and implement changes that result in more efficient use of resources. The lean approach encourages continuous improvement and focuses on delivering value to customers with minimal waste.
This philosophy often leads to a smoother, more streamlined operation that can quickly adapt to changing demands. Investigate how applying lean methodologies can transform your manufacturing process into a more efficient operation.
Increase Capacity by Retrofitting Machinery
To address significant production bottlenecks, manufacturing engineers may opt to retrofit existing machinery. By upgrading components or adding new technology to older machines, the production capacity can be increased without the need for costly new equipment. Retrofits can enhance the speed and efficiency of manufacturing processes, enabling a faster throughput that keeps pace with market demands.
This solution can often be implemented more quickly than replacing entire systems. Look into how retrofitting your machinery could unlock higher production rates and better performance.
Enable Parallel Operations for Efficiency
One innovative strategy to tackle manufacturing hold-ups is redesigning processes to enable parallel operations. By allowing tasks to be performed simultaneously, rather than sequentially, production time can be greatly reduced. This requires a comprehensive analysis and possibly reconfiguration of the production line but can lead to significant improvements in output rates.
By breaking down complex tasks into simpler, concurrent steps, manufacturers can significantly accelerate the production cycle. Evaluate your current processes to see if there are opportunities to implement parallel operations, thus improving productivity.
Prevent Bottlenecks with Predictive Maintenance
Predictive maintenance is an effective way manufacturing engineers can reduce downtime and prevent bottlenecks before they occur. Through the use of sensors and advanced analytics, potential issues with machinery can be anticipated and addressed proactively. This approach ensures that machines are serviced precisely when needed, avoiding both unexpected breakdowns and unnecessary preventative actions.
Regular maintenance based on predictive data can extend the life of equipment and maintain a steady flow of production. To maintain optimal production levels, consider adopting predictive maintenance practices.