7 Methods to Track Manufacturing Process Optimization Over Time
Discover the key to mastering manufacturing optimization with practical strategies that stand the test of time. This article distills the wisdom of industry leaders, offering proven methods to measure and enhance efficiency, quality, and sustainability in the production process. Equip yourself with the tools and knowledge to stay ahead in a competitive manufacturing landscape.
- Track Efficiency, Quality, and Sustainability Metrics
- Use Real-Time Monitoring and IoT Sensors
- Benchmark Against Industry Standards
- Analyze Production Cost Trends
- Monitor Adherence to Production Schedules
- Track Customer Satisfaction with Product Quality
- Measure Overall Equipment Effectiveness
Track Efficiency, Quality, and Sustainability Metrics
At Essential Workwear, we track and measure our manufacturing process optimization through a mix of efficiency, quality, and sustainability metrics. Key indicators include order turnaround time, production accuracy, defect rates, and waste reduction-all crucial in workwear production and customization.
We rely on real-time production tracking software to monitor output at every stage, from embroidery and printing to final dispatch. Monthly reports analyze first-time-right percentages, ensuring designs and custom branding meet client specifications without rework. Additionally, machine downtime tracking helps us proactively maintain equipment, minimizing delays. Since implementing these measures, we've improved production efficiency by 28% year-on-year while reducing material waste by 15%.
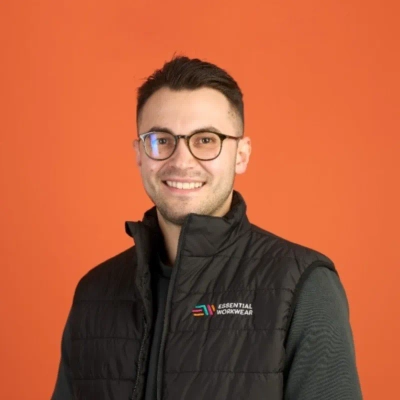
Use Real-Time Monitoring and IoT Sensors
The manufacturing clients we work with track optimization progress by focusing on **key efficiency metrics** like OEE (Overall Equipment Effectiveness), cycle time, and defect rates. The best approach? **Real-time monitoring with IoT sensors and AI-driven analytics.** Instead of waiting for monthly reports, they get instant insights into bottlenecks and downtime. One client cut waste by 20% just by using automated reporting dashboards to spot inefficiencies faster. The key is **continuous tracking, not just periodic check-ins**—if you're only measuring after the fact, you're already behind.
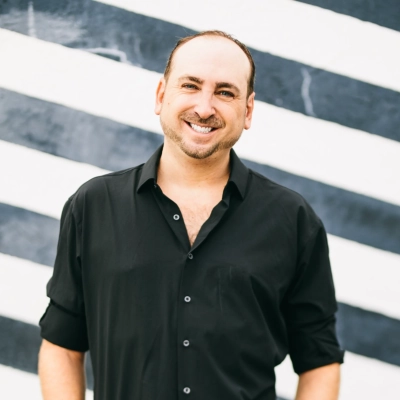
Benchmark Against Industry Standards
Benchmarking against industry standards allows businesses to understand their position in the market relative to competitors. By keeping an eye on these benchmarks, manufacturing processes can be fine-tuned to meet or even exceed the industry's best practices. This approach helps in identifying areas needing improvement and setting realistic goals.
Through regular comparison, companies can see where they stand and adapt accordingly. Stay up-to-date with industry trends to ensure your processes remain competitive.
Analyze Production Cost Trends
Analyzing production cost trends is an effective strategy to track how optimization efforts are impacting the bottom line. By regularly reviewing these costs, businesses can identify inefficiencies and areas where expenses can be reduced. Over time, this analysis can reveal patterns that help in making more informed decisions.
Understanding cost movements is vital in maintaining profitability and sustainability. Make it a routine to analyze cost data to drive continuous improvement.
Monitor Adherence to Production Schedules
Monitoring adherence to production schedules is crucial for maintaining operational efficiency. Meeting deadlines consistently ensures that the manufacturing process is running smoothly and that products are delivered on time. Delays can be costly and result in dissatisfied customers, which is why tracking this metric is essential.
Through close monitoring, areas causing delays can be identified and rectified promptly. Focus on adhering to schedules to boost overall process efficiency.
Track Customer Satisfaction with Product Quality
Tracking customer satisfaction with product quality provides insight into how well the manufacturing process meets consumer expectations. Positive feedback indicates that processes are effective, while negative feedback highlights areas needing improvement. This metric helps in aligning production practices with customer needs, which is vital for business growth.
Regularly gauging customer satisfaction ensures that products continue to meet high standards. Prioritize customer feedback to enhance product quality.
Measure Overall Equipment Effectiveness
Measuring overall equipment effectiveness (OEE) offers a comprehensive view of the efficiency of manufacturing processes. OEE combines data on availability, performance, and quality to give a clear picture of productivity. High OEE scores indicate that equipment is being used optimally, leading to better output.
Regular assessment of OEE can pinpoint issues impacting efficiency and guide corrective actions. Keep track of OEE to ensure your equipment and processes are functioning at their best.