6 Lessons from Successful Manufacturing Quality Audits
Navigating the complexities of manufacturing quality audits requires a strategic approach. This article unveils core strategies that drive efficiency and improve standards, from harnessing data for continuous improvement to engaging the workforce in proactive risk management. Discover how embracing technology and standardizing processes can unlock higher levels of quality and production excellence.
- Identify Assembly Line Inefficiencies
- Use Data for Continuous Improvement
- Engage Workforce in Quality Audits
- Standardize Processes for Consistent Quality
- Prioritize Proactive Risk Management
- Embrace Technology for Enhanced Quality
Identify Assembly Line Inefficiencies
Finding assembly line inefficiencies that resulted in a high failure rate was one of the effective quality audits I carried out in a manufacturing environment. We found that a particular machine calibration problem was the source of inconsistent product dimensions by examining production data and performing root cause analysis. Defect rates decreased by 35% in three months following the implementation of automated quality inspections and the improvement of standard operating procedures. The main conclusion was that real-time monitoring and proactive audits can stop flaws before they become more serious, increasing productivity and product quality.
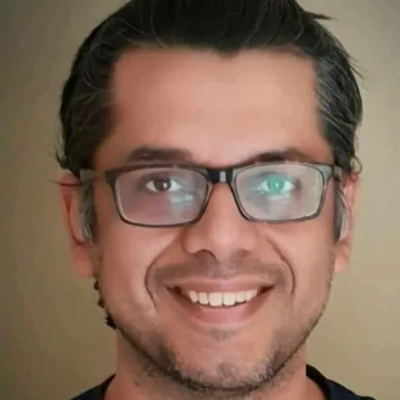
Use Data for Continuous Improvement
Using data to drive continuous improvement is essential. Quality audits often reveal areas for improvement, and data provides the evidence needed to make informed decisions. By analyzing trends and patterns, companies can identify root causes and implement effective solutions.
Success in manufacturing relies on making data-driven changes that enhance processes and products. Regularly reviewing data ensures that improvements are sustained. Start leveraging data today to boost your manufacturing quality.
Engage Workforce in Quality Audits
Engaging the entire workforce is key to a successful quality audit. When employees at all levels are involved, they are more likely to take ownership of the process. This collective effort helps ensure that quality standards are understood and maintained across the organization.
Encouraging open communication and feedback from staff can lead to innovative solutions for quality issues. Everyone in the company should have a role in quality assurance. Rally your team to participate actively in the next audit.
Standardize Processes for Consistent Quality
Standardizing processes and procedures is fundamental for consistent quality. Quality audits highlight the importance of having clear and standardized protocols. These standards help reduce variability and ensure that everyone follows the same guidelines.
Consistency in processes leads to fewer errors and higher quality products. It's crucial to document and regularly update procedures based on audit findings. Commit to standardizing your processes for better quality outcomes.
Prioritize Proactive Risk Management
Proactive risk management should be a priority in manufacturing. Quality audits often uncover potential risks before they become significant problems. By identifying risks early, companies can implement preventive measures to avoid costly defects and production delays.
Effective risk management involves continuous monitoring and assessing potential threats to quality. Staying ahead of risks ensures smoother operations and higher customer satisfaction. Take steps today to integrate proactive risk management into your quality strategy.
Embrace Technology for Enhanced Quality
Embracing technology and automation can significantly enhance manufacturing quality. Quality audits show that automated systems often perform tasks more consistently and accurately than humans. Implementing technology can streamline processes, reduce errors, and increase efficiency.
Innovations such as AI and machine learning offer predictive insights that can prevent quality issues before they arise. Investing in the latest technology is essential for staying competitive in the manufacturing industry. Consider upgrading your systems to harness the power of automation.