6 Key Performance Indicators (Kpis) for Tracking Manufacturing Quality
In the world of manufacturing, quality is paramount. Key Performance Indicators (KPIs) serve as crucial tools for measuring and improving production processes. This article explores six essential KPIs that can significantly enhance manufacturing quality and operational efficiency.
- First Pass Yield Drives Quality Improvements
- Defect Rate: Key to Manufacturing Excellence
- Customer Rejection Rate Enhances Product Quality
- Right First Time Boosts Production Efficiency
- Process Capability Index Ensures Manufacturing Consistency
- Overall Equipment Effectiveness Optimizes Manufacturing Operations
First Pass Yield Drives Quality Improvements
One crucial KPI for gauging quality performance in manufacturing settings is the First Pass Yield (FPY). This metric measures the percentage of products that meet quality standards without requiring any rework. By focusing on FPY, manufacturers can identify which stages of the production process are prone to errors and require adjustments. Monitoring FPY not only helps in ensuring that the final product meets customer expectations, but it also significantly reduces waste and increases efficiency.
To make the most out of the FPY, it's essential to regularly analyze the data and pinpoint specific areas where production might be falling short. For example, if a particular assembly line consistently shows a lower FPY, it might indicate a need for better training for operating personnel or improvements in machine maintenance. By addressing these issues, manufacturers can improve FPY rates, which in turn enhances overall manufacturing quality and reduces costs associated with reworks and scrap. Continuously tracking this KPI and implementing strategic changes based on its trends allows manufacturing managers to maintain a high standard of quality in their production processes.
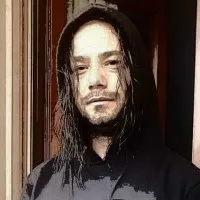
Defect Rate: Key to Manufacturing Excellence
Defect Rate is a crucial indicator for tracking manufacturing quality. It measures how often imperfections occur in products during the production process. By monitoring this rate, companies can identify issues in their manufacturing processes and work to reduce errors.
A lower defect rate typically indicates higher overall quality and can lead to increased customer satisfaction. Managers should regularly review defect rate data to spot trends and implement improvements. Take action today to start measuring and reducing your defect rate for better product quality.
Customer Rejection Rate Enhances Product Quality
Customer Rejection Rate is an important metric for assessing manufacturing quality from the end-user perspective. This indicator tracks the number of items returned by customers due to faults or defects. A high rejection rate may signal issues with quality control or product design that weren't caught during the manufacturing process.
By focusing on reducing this rate, companies can improve customer satisfaction and reduce costly returns. Regular analysis of customer feedback on rejected items can provide valuable insights for improvement. Start tracking your customer rejection rate now to enhance your product quality and customer experience.
Right First Time Boosts Production Efficiency
Right First Time is a key performance indicator that focuses on production efficiency without errors. This metric measures the percentage of products that are made correctly on the first attempt, without needing rework or corrections. A high Right First Time rate suggests a well-controlled and efficient manufacturing process.
Improving this indicator can lead to reduced waste, lower costs, and faster production times. Companies should strive to increase their Right First Time rate through better training, process improvements, and quality control measures. Begin monitoring your Right First Time rate to drive efficiency in your manufacturing process.
Process Capability Index Ensures Manufacturing Consistency
The Process Capability Index is a statistical measure used to assess the stability and consistency of a manufacturing process. This index compares the actual output of a process to its specified limits, indicating how well the process meets the required standards. A higher Process Capability Index suggests that a manufacturing process is more reliable and less likely to produce defects.
By regularly calculating and analyzing this index, companies can identify areas for improvement and make data-driven decisions to enhance their manufacturing quality. Start using the Process Capability Index to gain deeper insights into your production processes and drive continuous improvement.
Overall Equipment Effectiveness Optimizes Manufacturing Operations
Overall Equipment Effectiveness is a comprehensive indicator that monitors the quality performance of manufacturing machinery. This metric combines three key factors: availability, performance, and quality rate of the equipment. By tracking Overall Equipment Effectiveness, companies can identify bottlenecks, reduce downtime, and improve the overall efficiency of their manufacturing operations.
A higher score in this indicator often correlates with better product quality and increased productivity. Regular monitoring and analysis of Overall Equipment Effectiveness can lead to significant improvements in manufacturing output and quality. Implement a system to measure and improve your Overall Equipment Effectiveness for better manufacturing results.