5 Tools to Improve Communication Between Shop Floor and Business Systems
Unlock the potential of seamless communication between the shop floor and business systems with proven strategies from industry experts. Discover tools that not only enhance real-time collaboration but also integrate critical business operations for efficiency and growth. Dive into the expertise that guides you through the transformation of manufacturing communication, without the complexity.
- CRM-ERP Integration Streamlines Business Operations
- Trello Boosts Real-Time Shop Floor Communication
- Tulip Platform Bridges Shop Floor-ERP Gap
- Trello Enhances Global Business Collaboration
- MES Software Transforms Manufacturing Communication
CRM-ERP Integration Streamlines Business Operations
One tool that has significantly improved communication between our shop floor and business systems is CRM integration with our ERP system. In this case, we integrated Salesforce with Odoo.
By integrating our CRM with our ERP, approved client sales are automatically logged in our ERP. Our salespeople don't have to inform accounting, and accounting doesn't have to badger our sales team for details. The baton is passed perfectly by the data connector.
This integration transformed operations by streamlining workflows, improving data accuracy, and eliminating administrative burdens. With real-time data flow between systems, both frontline staff, finance, and leadership operate with full visibility, allowing for faster decision-making and a more agile business.
Trello Boosts Real-Time Shop Floor Communication
One specific tool that has significantly improved communication between our shop floor and business systems is Trello. We use it to track tasks and communicate in real-time between departments, especially when it comes to production schedules and inventory management. Before implementing Trello, our team relied on emails and paper-based systems to communicate updates, which led to miscommunication and delays. With Trello, each department can update their progress on tasks directly on the board, and everyone--from the shop floor to the management team--can see updates instantly.
For example, when there's a delay in production, the team can immediately update the card on Trello, and I get an instant notification. This has allowed us to address issues much more quickly and adjust workflows as needed. The tool has created a more transparent and efficient communication loop, ensuring that everyone is on the same page and helping us reduce downtime and improve productivity across the board.
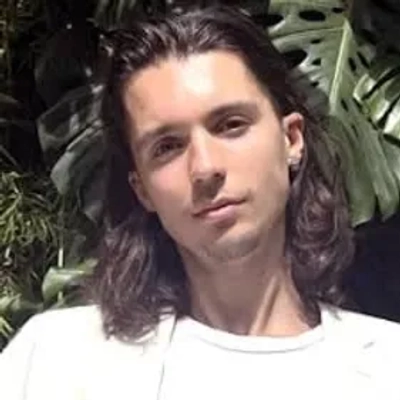
Tulip Platform Bridges Shop Floor-ERP Gap
One specific tool that has significantly improved communication between our shop floor and business systems is Tulip -- a frontline operations platform built for real-time data capture and integration.
Why it made a difference:
Before Tulip, there was a clear disconnect between floor activity and our ERP system. Data was often delayed, handwritten, or manually entered -- leading to inefficiencies, blind spots, and reactive decision-making.
With Tulip, we implemented custom digital workstations that allow operators to log production data, quality checks, and downtime events in real time. This information syncs instantly with our business systems and integrates seamlessly with sensors and machines, providing live visibility into shop floor performance.
The impact:
• Reporting lag dropped from hours to minutes
• First-pass yield and quality control improved measurably
• Production planning and inventory became more precise
• Operator engagement increased through intuitive, no-code interfaces
For manufacturers looking to bridge the gap between their shop floor and business systems -- without overhauling their entire tech stack -- platforms like Tulip are a transformative solution.
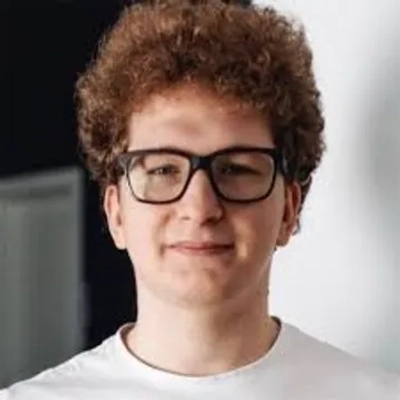
Trello Enhances Global Business Collaboration
One online tool that has been particularly helpful in managing our international business operations is Trello. It has streamlined our processes by providing a simple, visual way to track tasks and collaborate across time zones. With Trello's boards, lists, and cards, we can assign responsibilities, set deadlines, and ensure that everyone on our global team is aligned. This tool has been invaluable in keeping projects organized, especially when coordinating with partners or clients from different parts of the world.
The feature I'd highly recommend is Trello's integration with other apps like Slack, Google Drive, and Jira. This connectivity allows us to centralize all communications and project documents in one place, making information easily accessible to everyone involved. It also helps us stay agile and responsive to any challenges, whether they're logistical, financial, or client-related. Trello has enhanced our efficiency by simplifying workflows and ensuring seamless coordination across multiple departments and regions.
MES Software Transforms Manufacturing Communication
One tool that has proven invaluable in bridging the gap between shop floors and business systems is MES, or Manufacturing Execution Systems. This software provides a real-time, interactive platform that supports the manufacturing process from start to finish. By integrating MES with ERP systems, businesses achieve smoother operations, timely data updates, and more synchronized workflows. The ability for front-line managers to monitor and react to shop floor events instantaneously, combined with the capability to track production against corporate objectives, transforms operational efficiency and reduces communication latency.
The impact of MES can be seen in environments like automotive manufacturing plants where the need for precision and timing is critical. For instance, a major car manufacturer implemented an MES and experienced a noticeable improvement in the way information flowed from the shop floor to the top floor. This enhancement in data visibility helped reduce the production cycle time and increase the overall equipment effectiveness (OEE). Such tools not only provide clear communication channels but also foster a culture of data-driven decision making, which is essential in today's competitive market. Ultimately, a well-implemented MES system can turn a bustling shop floor into a major information hub, supporting continuous improvement and strategic business growth.
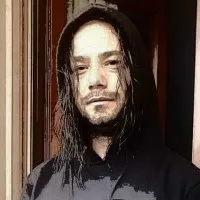